MP Filtri, la pulizia dei sistemi oleodinamici e la resilienza aziendale. Intervista a Massimiliano Sanna
Nel settore industriale i processi di pulizia che interessano i sistemi oleodinamici – anche del comparto agricolo – rivestono un ruolo sempre più cruciale. Soprattutto, nel delicatissimo momento dell’avvio del macchinario, dopo l’assemblaggio finale. Un processo da più di cinquant’anni al centro degli sforzi progettuali e produttivi di MP Filtri, storica realtà nel milanese, tra […]

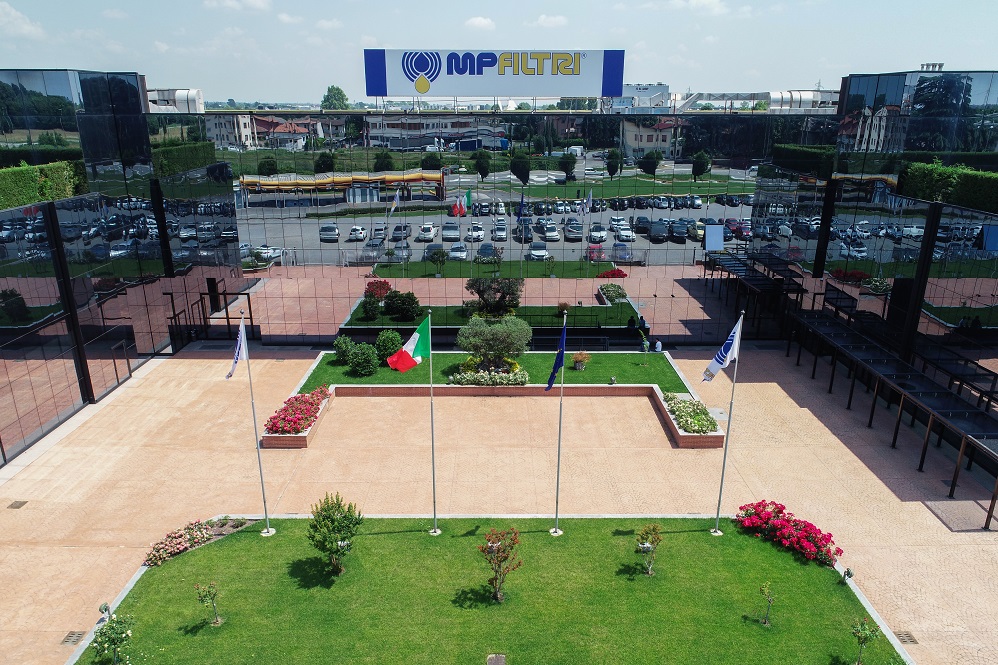
Nel settore industriale i processi di pulizia che interessano i sistemi oleodinamici – anche del comparto agricolo – rivestono un ruolo sempre più cruciale. Soprattutto, nel delicatissimo momento dell’avvio del macchinario, dopo l’assemblaggio finale.
Un processo da più di cinquant’anni al centro degli sforzi progettuali e produttivi di MP Filtri, storica realtà nel milanese, tra i leader in questo settore. Per approfondire le tematiche che ruotano intorno all’oleodinamica, e fare il punto sulle strategie aziendali alla luce degli stravolgimenti portati dalla pandemia di Covid-19, abbiamo parlato con l’ing. Massimiliano Sanna.
Buongiorno Ingegner Sanna, prima di iniziare potrebbe illustrare ai nostri lettori il suo ruolo all’interno di MP Filtri?

Da 4 anni ricopro il ruolo di Marketing Manager per il Gruppo MP Filtri, con la responsabilità di coordinare e supervisionare tutte le attività di Marketing e Comunicazione per l’HQ e le Filiali, oltre che fornire il supporto necessario per tutte le attività di joint marketing con i nostri partner commerciali.
Alla luce degli stravolgimenti portati dalla pandemia di Covid-19, come ha reagito e che strategie ha messo in campo MP Filtri?
Il primo lock-down ci ha colti un po’ impreparati, come quasi tutte le aziende italiane. Fortunatamente però MP Filtri era già strutturata per soddisfare la maggior parte dei requisiti e delle prescrizioni imposte dai vari DPCM, come gli accessi separati ed il distanziamento sia negli uffici che in produzione. Non appena possibile, infatti, siamo stati subito in grado di ripartire senza modifiche sostanziali con la normale attività manifatturiera facendo parte della filiera produttiva di quei settori considerati essenziali.
Per poter riaprire anche gli uffici di MP Filtri, pur se con presenza limitata in funzione del numero di dipendenti presenti in ogni locale, attivando le modalità di smart working dove e quando possibile, abbiamo dovuto solo implementare: la sanificazione degli ambienti in aggiunta alle normali operazioni di pulizia, la collocazione di vari dispenser con soluzione alcolica in giro per l’azienda, una diversa modalità di accesso e gestione del servizio mensa.
Ci sono stati poi altri sostanziali cambiamenti. Abbiamo bloccato da subito tutte le trasferte (in Italia ed Estero), annullato tutti i meeting e gli eventi interni ed esterni, così come limitato al massimo le visite di fornitori presso le nostre sedi. Chiaramente abbiamo subito reperito le mascherine chirurgiche, FFP2 ed FFP3, da fornitori qualificati e riconosciuti dall’Istituto Superiore della Sanità, per dotare tutti i dipendenti dei DPI aggiuntivi, obbligatori all’interno dell’azienda.
Dal punto di vista delle attività strategiche e degli investimenti, gli unici rallentamenti sono stati dati da stakeholders esterni all’azienda (organizzazioni governative locali e nazionali, impedimenti e limitazioni lavorative per i fornitori imposte dai vari DPCM, e così via). Fortunatamente, infatti, il nostro calo di fatturato è dovuto solamente alle settimane di lockdown totale imposto dai Governi locali alle varie sedi del Gruppo dislocate in giro per il mondo.
Nonostante la situazione sicuramente non rosea, siamo stati comunque in grado di completare il nuovo stabilimento produttivo a Filadelfia negli USA e lo spostamento della nostra sede a Shanghai in Cina in una location più adatta, con trasloco e ripartenza di tutte le normali attività lavorative in entrambe le sedi.
Vista l’impossibilità di incontrare direttamente la maggior parte dei clienti, ci siamo attivati “digitalmente” implementando nuovi canali social, coordinati dal punto di vista grafico e del layout a livello Corporate (per le filiali in particolare per USA, UK, Francia e India). A partire da Settembre abbiamo poi cominciato ad essere invitati e coinvolti in diversi webinar come relatori, cui abbiamo aderito con piacere. Per ultimo, abbiamo anche accelerato la realizzazione di un nuovo sito internet completamente rivisitato nei contenuti, con nuovi servizi e nuove sezioni che ci permetteranno di essere più vicini ai nostri clienti. Il nuovo sito web è stato pubblicato ad inizio Dicembre.
Come procedono i lavori all’interno del vostro centro Ricerca & Sviluppo, inaugurato tre anni fa, fiore all’occhiello della sede di Pessano? Sono in previsione ulteriori ampliamenti o nuovi progetti? Nel caso potrebbe darci qualche (piccola) indiscrezione?
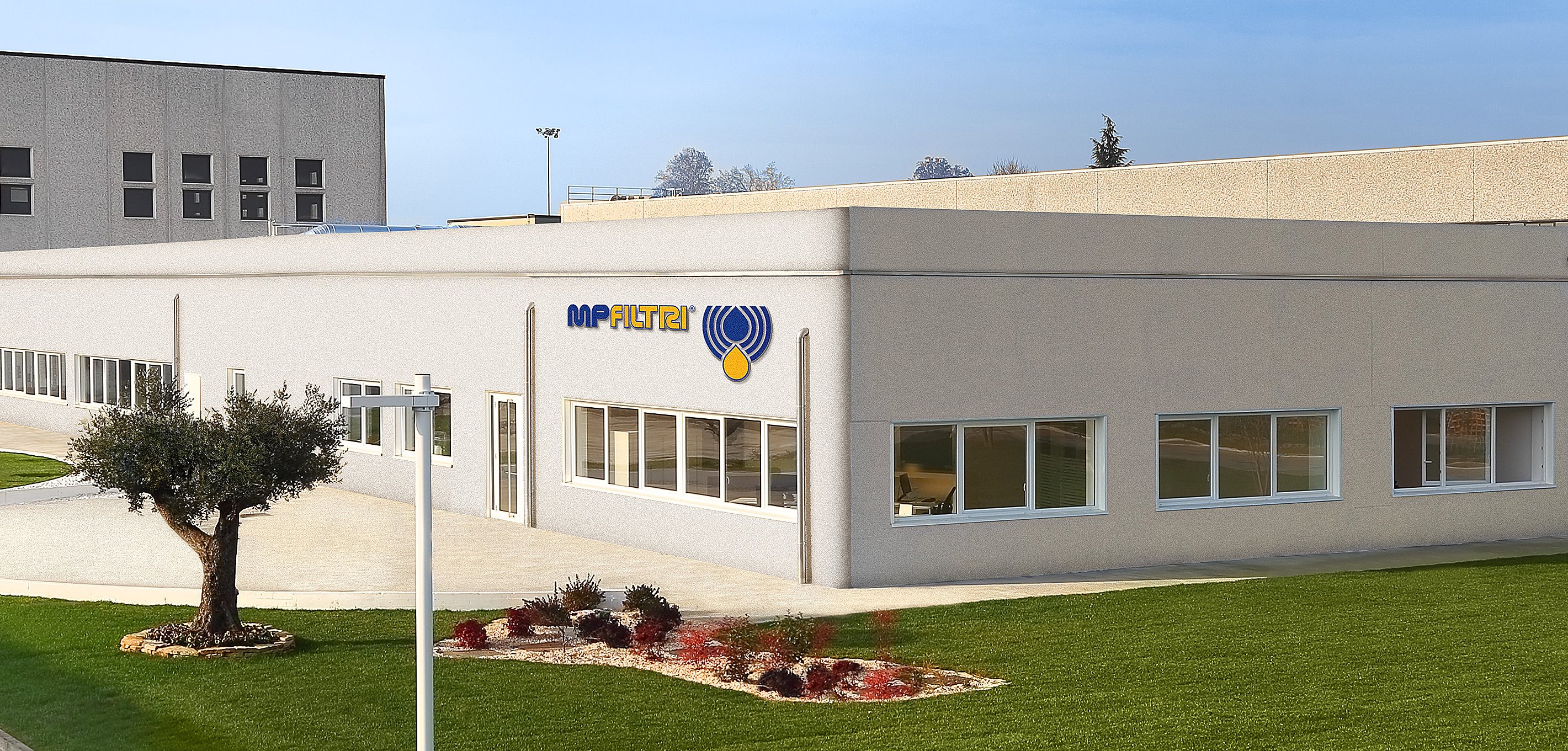
Il nostro Laboratorio continua ad essere un vero gioiello. La sua importanza e valenza si è dimostrata assolutamente strategica, consentendoci di fare enormi passi avanti per quanto riguarda nuovi materiali, la classificazione aggiornata secondo le ultime normative internazionali delle prestazioni dei nostri filtri ed elementi filtranti, lo studio della concorrenza e l’analisi di applicazioni speciali. A partire dall’anno scorso, poi, abbiamo incrementato la strumentazione con l’acquisto e l’installazione di altre tre nuove macchine:
- un banco per la prova di Collasso e Fatica dei filtri (pressione max 250 bar portata max 250 l/min), funzionante secondo test intasamento con ISO MTD ed operante per rispondere alle normative:
- ISO 3724: Hydraulic fluid power — Filter elements — Determination of resistance to flow fatigue using particulate contaminant
- ISO 3968: Hydraulic fluid power — Filters — Evaluation of differential pressure versus flow characteristics
- un banco per la prova di Fatica a pressione (pressione max 750 bar), per rispondere alla normativa:
- ISO 10771-1: Hydraulic fluid power — Fatigue pressure testing of metal pressure-containing envelopes
- un banco di portata adatto anche per operare con olio biodegradabile (pressione max 20 bar, portata max 200 l/min), predisposta per l’aggiunta di sistemi e dispositivi specifici atti alla misurazione delle prestazioni e caratteristiche di prodotti speciali (ad es. la misurazione delle cariche elettrostatiche o il fenomeno della deareazione, caratteristiche attualmente non normate), rispondente alla normativa:
- ISO 3968: Hydraulic fluid power — Filters — Evaluation of differential pressure versus flow characteristics
Pulizia Roll-off: in che cosa consiste? Quali sono le applicazioni in seno al mondo delle macchine agricole, della cava-cantiere e, più in generale, del settore della movimentazione terra che possono beneficiarne?
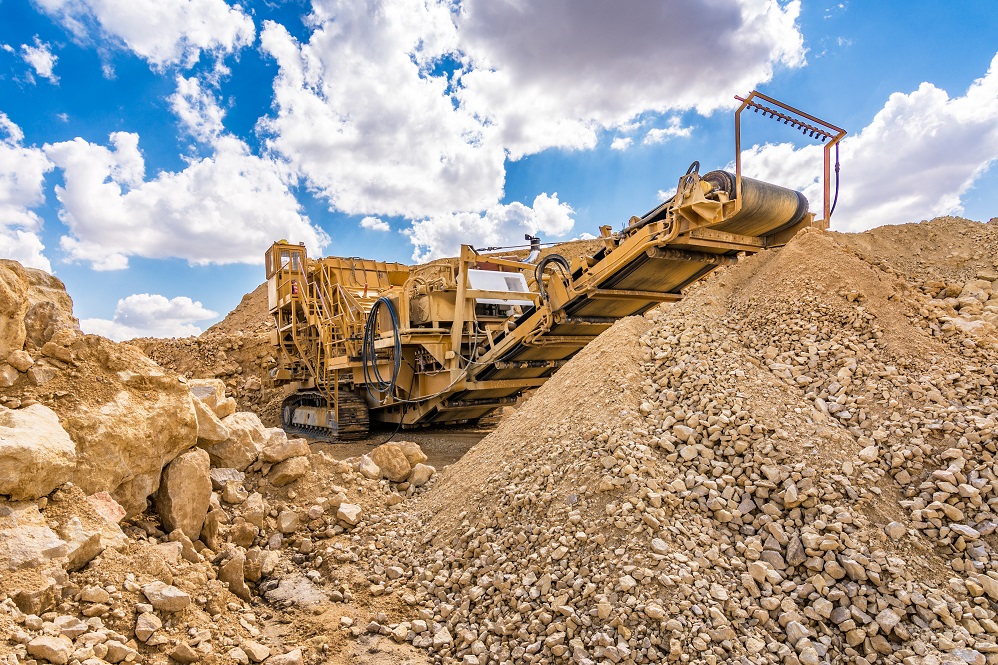
Lo scopo principale della pulizia “roll-off” consiste nel minimizzare i danni ai vari componenti del sistema all’inizio della loro vita. Per sottolineare l’importanza di questo tipo di pulizia, l’ISO = International Organization for Standardization sta sviluppando anche nuovi standard. Una bozza di questa nuova normativa, la ISO / WD 16431, descrive la pulizia ‘roll-off’ di un impianto idraulico assemblato dopo il rilascio dalla zona di produzione.
L’assemblaggio di una macchina è infatti una delle attività più critiche per quanto riguarda la pulizia nelle macchine e negli impianti oleodinamici, in quanto le varie parti non ancora montate ed in contatto tra di loro possono essere soggette a tutte le forme di contaminazione, a causa sia dell’ambiente che delle operazioni di montaggio stesse.

Quali sono le principali fonti di contaminazione su cui i prodotti di filtrazione devono lavorare?
In genere, le sorgenti di contaminazione possono essere caratterizzate come segue:
- Built-In: contaminazione involontaria lasciata nel sistema o in un componente durante l’assemblaggio iniziale o un intervento di manutenzione, come ad esempio piccoli pezzi di saldatura, polvere, fibre (provenienti ad esempio dagli stracci per la pulizia), trucioli di vernice e altre particelle indesiderabili e potenzialmente abrasive; molte di queste particelle sono al di sotto della soglia visiva umana di 40μm, ma sebbene non visibili possono essere comunque molto dannose per il sistema;
- Generato: contaminanti generati internamente durante il funzionamento del sistema, causati da usura, corrosione, agitazione/movimentazione di masse e fluidi, ossidazione o degradazione del fluido;
- Ingerito: contaminazione introdotta dall’esterno e che penetra in un sistema attraverso varie aperture come sfiatatoi, coperchi di accesso sigillati in modo errato, ma anche tergicristalli consumati, e così via.
Dunque contaminazione built-in. Quali sono i principali metodi di pulizia roll-off che si possono utilizzare? E quali sono le soluzioni che MP Filtri ha messo in campo per ovviare alle insidie che provengono dai contaminanti da particolato?
Esistono diversi modi per pulire un sistema (macchina o impianto) durante l’avviamento, ma spetta alla divisione manifatturiera dell’azienda decidere quale utilizzare in funzione della sua struttura ed organizzazione. L’obiettivo finale è comunque sempre quello di raggiungere il livello di pulizia desiderato al costo più ragionevole possibile ed in un intervallo di tempo minimo.
Ad esempio:
- Lasciar funzionare il sistema a bassa pressione durante il suo normale ciclo operativo, utilizzando i filtri già presenti nello stesso per questo primo processo di pulizia/lavaggio. Il vantaggio principale di questo metodo è la semplicità, in quanto non necessita di alcun dispositivo aggiuntivo. Tuttavia i filtri del sistema potrebbero non avere una capacità di trattenimento dello sporco sufficiente per durare tutto il processo di pulizia e potrebbero essere necessarie diverse sostituzioni degli elementi filtranti per pulire completamente un sistema sporco. Questo metodo però potrebbe anche danneggiare alcuni componenti critici del sistema se il livello di contaminazione iniziale fosse troppo alto.
- SOLUZIONE MP FILTRI: Filtri della nostra gamma standard in aspirazione, in linea, nel ritorno
- Utilizzare un’unità mobile di filtrazione, a volte indicata come “filter buggy” (filtro difettoso in italiano) o “kidney loop” (circolo renale in italiano, seguendo l’idea della dialisi renale). Questa unità mobile e autonoma filtra il fluido offline utilizzando la propria pompa, motore e filtro ed è progettata per funzionare a bassa pressione, generalmente inferiore a 100 psi = 6,89 bar. Il modo migliore per utilizzare questa macchina esterna è collegare i tubi di aspirazione e di ritorno al serbatoio del sistema attraverso dei raccordi specifici e lasciarla lavorare secondo suo ciclo mentre il sistema funziona a bassa pressione; l’olio che ritorna al serbatoio dalla linea di ritorno verrà quindi filtrato attraverso l’unità mobile. Questo processo offline integra i filtri già presenti nel sistema, riducendo notevolmente i tempi di pulizia.
- SOLUZIONE MP FILTRI: Le nostre unità mobili di filtrazione UFM
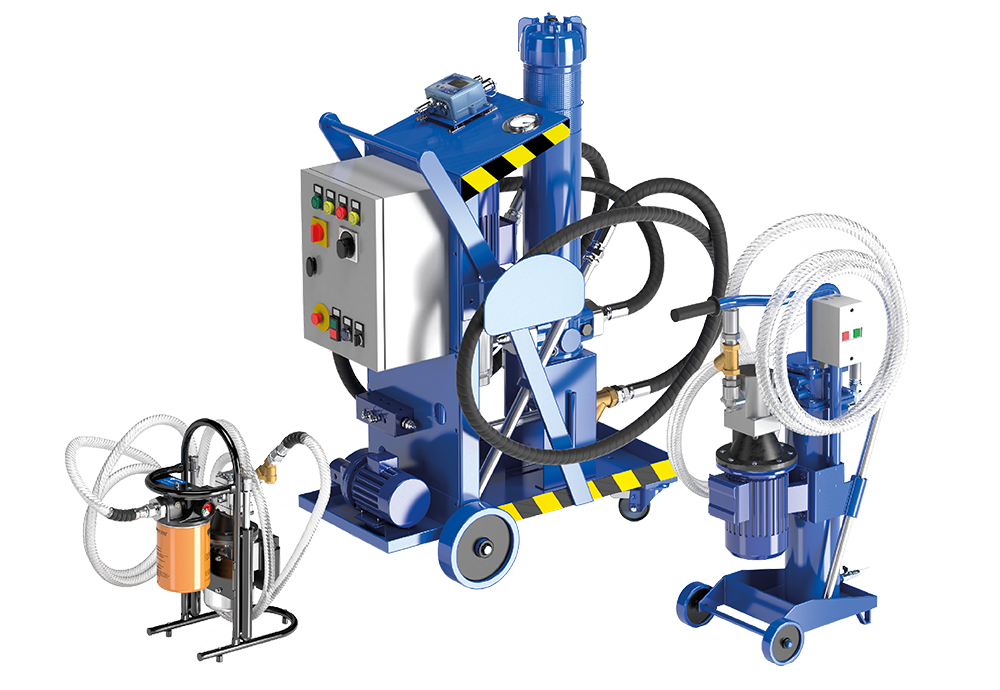
- Progettare ed impiegare un filtro offline, opportunamente dimensionato, che può essere collegato al sistema alla pressione di lavoro dello stesso in modo tale da divenire l’alimentazione del sistema stesso. In questo caso l’apparecchiatura può essere messa in funzione utilizzando l’energia idraulica del sistema offline. Non è necessario mettere in funzione il sistema principale se non per rimuovere l’olio dalle linee che non sono in circolazione e che la portata del filtro offline sia grande quanto quella del sistema. L’idea è quella di mettere in ciclo il sistema a scopo di lavaggio (“flushing”) ma non necessariamente alla stessa velocità operativa normale. Quest’ultimo metodo riduce al minimo i danni ai componenti del sistema.
- SOLUZIONE MP FILTRI: Utilizzare i nostri filtri serie LMP 400, LMP 430 e LMP 950, oppure la serie LMP 900 con elementi filtranti secondo DIN 24550 per la costruzione di un sistema off-line opportunamente dimensionato
Non è economicamente plausibile rimuovere tutti i contaminanti da un sistema, anche perché la maggior parte dei sistemi funziona senza problemi anche con una piccola quantità di contaminazione presente. Questo quantitativo di contaminante solido tollerato in un sistema dipende dalla sensibilità del componente più critico; tutti i costruttori di componenti e dispositivi oleodinamici indicano infatti il valore massimo di contaminante espresso come classe di contaminazione secondo la normativa ISO 4406. Le dimensioni e il tipo di filtro o di unità mobile utilizzati sono fondamentali per eseguire correttamente i calcoli sulla pulizia roll-off da contaminazione built-in di un sistema oleodinamico. L’affidabilità del sistema continuerà a migliorare fino a quando vengono raggiunte le condizioni ideali.
Quali sono i benefici apportati ai macchinari da una corretta filtrazione?
Le corrette procedure di pulizia “roll-off” proteggono l’impianto dalla nascita e consentono un numero inferiore di reclami in garanzia. Al cliente finale viene fornito un sistema di alta qualità con componenti puliti che soddisfano le sue esigenze di utilizzo finale.
La pulizia “roll-off”, tuttavia, è solo il punto di partenza per un funzionamento del sistema senza problemi. La responsabilità finale nel controllo della contaminazione spetta all’utilizzatore che deve mantenere un adeguato livello di filtrazione e praticare un controllo responsabile della contaminazione nel sistema per mantenere pulito il fluido e, di conseguenza, tutto il circuito oleodinamico. Meglio se utilizzando anche dei dispositivi di controllo della contaminazione (ad esempio i nostri contatori di particelle) per verificare con esattezza il livello di contaminazione presente nel sistema, e degli indicatori di intasamento differenziali su ogni filtro per operare tutti gli interventi di manutenzione preventiva necessari a mantenere il giusto grado di filtrazione.
I benefici apportati ai macchinari da una corretta filtrazione sono molteplici, primo fra tutti la perfetta funzionalità ed operatività, evitando o riducendo guasti o danneggiamenti incontrollati e imprevedibili. Che alla fine si traduce in una vita allungata dei macchinari stessi ed in un risparmio complessivo considerevole, se si tiene in considerazione il costo totale di esercizio.